The evolution of ultrasonic technology for smarter flow measurement
Release Time:2019-02-12 Reads:4997
In industrial markets, semiconductor chipsets play a huge role in the transformation of mechanical equipment to electromechanical or purely-electronic equipment. Every market segment is broken down into many applications, and silicon manufacturers spend time designing products specific to each application.
Technology advancements for any application usually comprise several smaller advancements that either happens sequentially or in parallel. For example, automation of an application typically requires the sensing of one or more parameters, followed by processing, which leads to control and/or communication. Technologically advanced sensors lead to enhanced money specifications such as higher performance, lower size, lower power, lower cost, and higher efficiency of the overall application. Similar advancements made to processing, types of control, and communication to the outside world will further enhance these money specifications.
Efforts to modernize the energy grid to make it more efficient, robust, and secure have led to an enormous increase in the use of electronics, thus opening up opportunities to innovate, increase functionality, and reduce size and cost. The energy conservation movement calls for integrating the conventional grid with the distributed grid to form the connected grid. Smart meters form an integral part of the power and energy sector, with over $2 billion of annual semiconductor total area market worldwide. Smart meters are further classified into electricity, water, gas, and heat meters.
Ultrasound or ultrasonic technology has been in use for over 100 years in several civil, medical, and military applications. Almost everyone has experienced medical ultrasonic technology in their lifetime; however, the most recent use cases have been in automation for the industrial and automotive markets. It’s amazing to see this technology find its place in a truly diverse set of applications. Ultrasonic technology’s noninvasive (noncorrosive) and contactless properties make it a perfect candidate for medical, pharmaceutical, military, and factory applications.
In the industrial and automotive segments, you’ll find ultrasonic technology used for distance measurement, occupancy detection, level detection, composition analysis, flow-rate measurement, parking assist, landing assist, and trunk open assist. Ultrasonic sensors, also known as ultrasonic transducers, operate outside the frequencies audible to humans and the frequencies are between 20 kilohertz to a few megahertz.
A majority of the ultrasonic transducers are constructed using a piezoelectric material, which when subject to electrical impulses respond with mechanical vibrations or ultrasound. Some transducers are also capable of converting mechanical vibrations back into electrical energy. Transducers are broadly classified into three types:
- Transmitters convert electrical signals into ultrasound.
- Receivers convert ultrasound into electrical signals.
- Transceivers can both transmit and receive ultrasound.
The postprocessing of received electrical signals results in several quantities relevant to the any industrial or automotive application. The most common and important quantity is ultrasonic time of flight (TOF), which is a round-trip time estimation of an ultrasonic wave emitted from a sensor to a targeted object, and then reflected from the object back to the sensor. This is the driving principle behind the use of ultrasonic technology in smart meters to measure the flow rates of water, gas, or heat (either intrusively or nonintrusively) and derive consumption data to bill consumers.
Flow measurement is the quantification (volume) of flow or the rate of flow for a liquid or gas, measured in units similar to liters per minute (or second or hour), or square meters per second. Flow meters range from simple utility meters (gas, water, heat) in homes to industrial gauges or mixers for hazardous liquids or gases (petroleum, mining, wastewater treatments, paints, chemicals).
Architecturally, a flow meter comprises a sensor unit, a measurement unit, and a control/communication unit. Each of these units can be further classified as mechanical or electronic. Figure 1 compares the different types of flow-meter sensing technologies that form a sensor unit. Ultrasonic-type flow meters have several advantages.
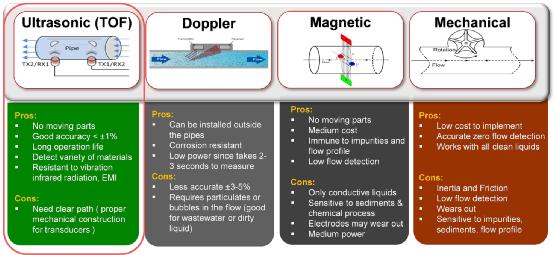
Figure 1 Comparison of sensing methodologies for liquid or gas flow
TOF-based or ultrasonic meters measure flow rates by calculating the difference in time (the propagation delay) of transmitted and received ultrasonic signals. In order to apply this to flow measurement, designers use a pair of identical transceiver-type transducers and excite them in the upstream and downstream directions. An ultrasound wave travels faster when traveling in the direction similar to the flow and slower in a direction against the flow. Hence, we require at least a pair of transducers; however, some topologies use more than two transducers.
Figure 2 shows a typical concept used in ultrasonic sensing for flow, with options for transducer placements in a pipe.
The choice of ultrasonic sensors depends on the type of medium that needs flow-rate measurement. Typically, liquid sensing uses sensors higher up in the frequency spectrum (>1 MHz), while gaseous media use sensors in the lower end of the frequency spectrum (< 500 kHz). Furthermore, ultrasonic technology for flow measurement requires a direct path between any two transducers, which requires careful mechanical construction of the flow tube housing the transducers. Ultrasonic technology does not work in the presence of air bubbles, which can lead to significant attenuation of the ultrasound signal.
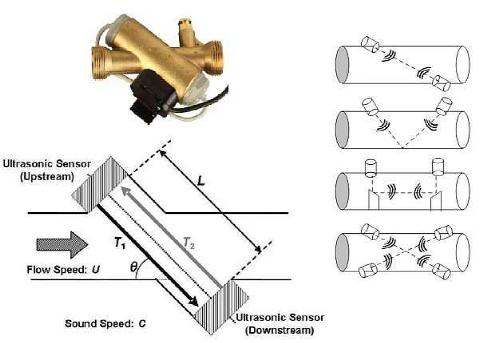
Figure 2 Examples of ultrasonic sensing for flow meters and common topologies for positioning within a pipe
Resource:https://www.edn.com/design/analog/4461515/The-evolution-of-ultrasonic-technology-for-smarter-flow-measurement